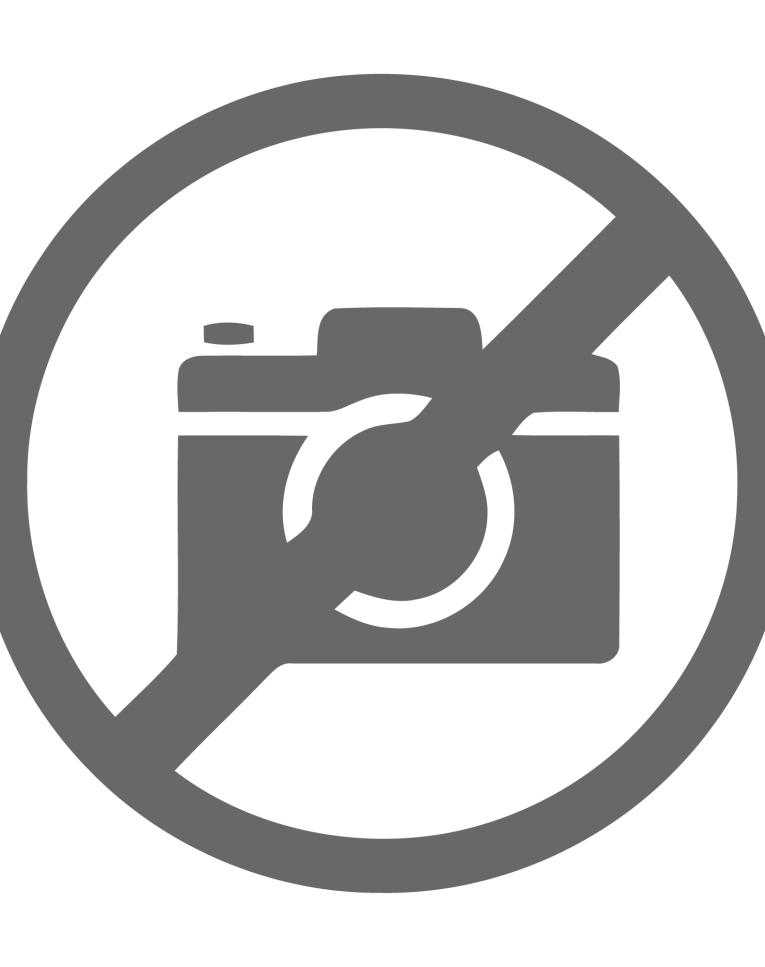
It is not hydroscopic and boasts high environmental tolerance. Endumax also provides high sensitivity, and smooth response. The stiffness for a given cone weight and geometry is greater than polypropylene and quality paper cones. From a speaker designer’s perspective, it is possible for extremely wide cone body angles (shallow cone), smaller voice coil diameters, and/or smaller magnetic systems to achieve comparable or superior results to existing speaker cone solutions (see Photo 1).
Speaker engineers know that three important physical properties determine a material’s suitability for use in loudspeaker diaphragms — stiffness, low density, and internal damping. Stiffness, in particular, determines the bending wave velocity, and for any given design, the frequencies at which the first breakup resonance occur. This resonance in a diaphragm determines the transition point above the frequency point at which the diaphragm loses piston motion and response becomes rougher.
The high Young modulus (and the steepness of the cone body angle and the diameter) determine at what point things become nasty. The degree of internal damping, or loss factor, determines the effectiveness of the material in suppressing such resonances, which is especially important near and above the upper resonance. Endumax absorbs extremely high amounts of energy. While this property was designed for ballistic protection products, the properties also make the material especially suited for speaker diaphragms as there will be less energy reaching the surround edge to reflect back.
The best materials will have high velocity and high damping, but for those who have used titanium cones and domes, you know that in many cases these properties are mutually exclusive.
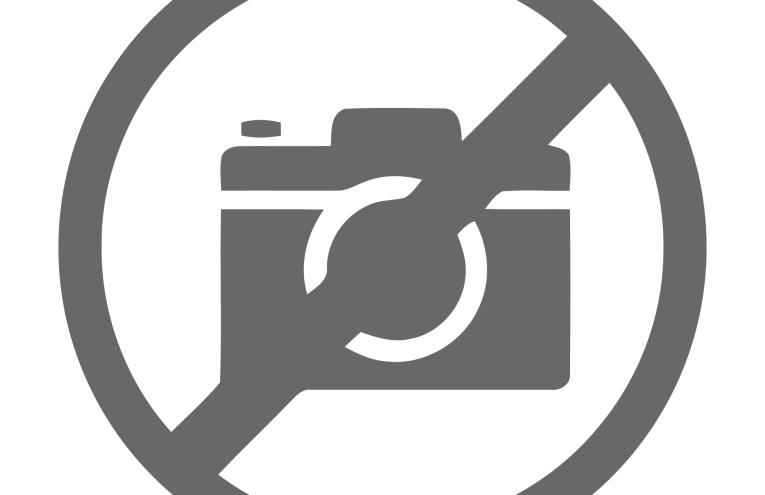
Endumax, which is similar to aramids such as Teijin Technora and DuPont Kevlar, offer a great combination of both damping and velocity. Materials like Endumax have low density so using multiple layers will result in a stiffer and stronger cone with low weight.
While no single material can be the perfect solution for every speaker diaphragm application, now we might have something that comes close. Young’s modulus (the speed of sound through the cone) and the internal damping (the mechanical loss coefficient) parameters of Endumax are off the charts. So who makes this amazing stuff?
Endumax was developed and manufactured by Teijin Aramid, a subsidiary of the Teijin Group. Teijin is a longterm supplier to the speaker industry. You may already be using Teijin’s Conex woven aramid fibers for your spiders and the material mixed into the paper pulp by your cone vendor might not be Kevlar but Twaron or Technora (both are comparable para aramids).
Teijin’s plants are located in The Netherlands and Japan. Endumax is made in The Netherlands. If your tweeter or headphone diaphragms use PEN film, it is likely from DuPont Teijin, a joint venture between the companies.
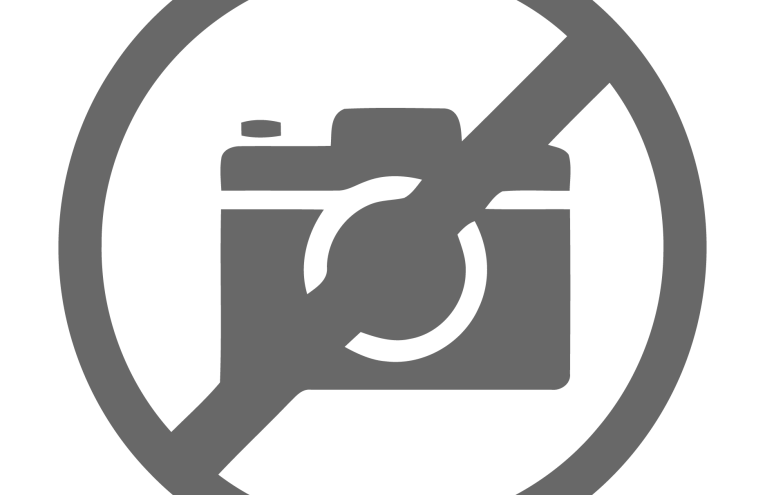
Forming Endumax
Forming Endumax requires preheat, a positive and negative mold, no-gap tooling, and a hydraulic press. Fast, shallow forming should be no problem, with deep shapes requiring more time to form. Ongoing development of deep draw material is in progress. An advantage of working with Endumax is its low “creep” (or more accurately “high dimensional stability” compared to other “self-reinforced” materials such as CURV) so that you will not have a lot of shrinkage in the pre-heating process.
Still, other related parameters are exceptional (e.g., the stiffness and the strength). The design rules for speakers utilizing Endumax are more flexible. A deep cone body angle and high mass are not needed to achieve stiffness. In fact, very shallow and even flat diaphragms can now achieve high excursions without excessive flex or cone creasing. Deep bass subwoofers can work in-wall, high performance autosound speakers can be surface mounted.
Material Science
Endumax is a thin, ultra-strong highly oriented (highly crystalline) tape. It has excellent resistance to water, moisture, most chemicals, UV light, and microorganisms. Unlike some fibers originally intended for anti-ballistic applications, Endumax does not swell or hydrolyze in water, sea water, or moisture. The tenacity is extraordinary and far higher that of a good quality steel. The Young’s modulus is very high, much higher than Kevlar 29, 49, and even higher than the military grades. The material is second only to that of esoteric carbon fiber grades (see Table 1). It is suitable for applications ranging from force transmission, material reinforcement, and rope connections to ballistic protection and speaker cones. It is 11 times stronger than steel, on a weight-for-weight basis, yet it boasts low density. It floats on water.
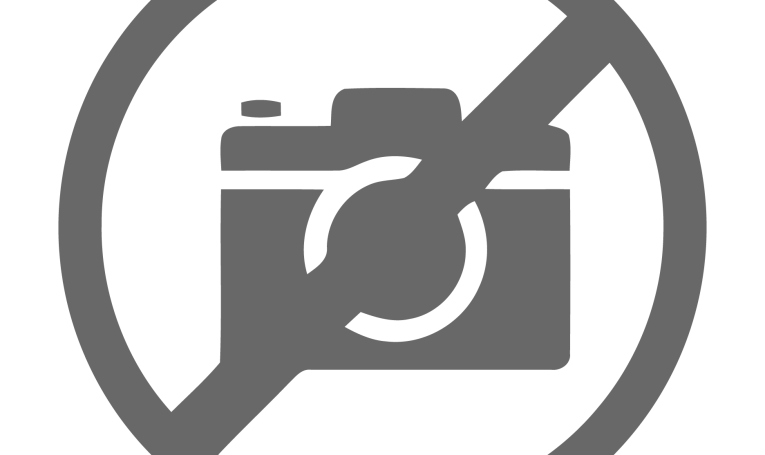
Endumax is an ultra-high-molecular-weight polyethylene (UHMWPE), an engineering plastic subset of the thermoplastic polyethylene (see Photo 2 and Photo 3). This family also includes as high-modulus polyethylene (HMPE) or high-performance polyethylene (HPPE). They have extremely long molecular chains that serve to transfer load more effectively to the polymer backbone by strengthening intermolecular interactions. This results in a very tough material, with the highest impact strength of any thermoplastic.
UHMWPE is odorless, tasteless, has no solvents, and is nontoxic. It is highly resistant to a wide range of chemicals. It also has extremely low moisture absorption and a very low coefficient of friction. The material is self-lubricating and highly resistant to abrasion.
Thermal Stability
Endumax’s stiffness and tensile strength is reduced above 70°C (158°F) onwards because the material starts to soften a bit. From 70°C to 135°C, the deterioration of the mechanical properties is reversible and the upper end of the temperature range is used for part forming. Specifically this means that when the temperature drops down to 70°C or lower, the mechanical properties are fully back on track again.
This recovery factor and wide temperature margin between heating to soften the material to form it and the heat damage temperature range, enables practical heat-forming techniques that will not degrade the shaped part. The mechanical properties do not deteriorate at extremely low temperatures and Endumax will never become brittle such as with many types of plastics.
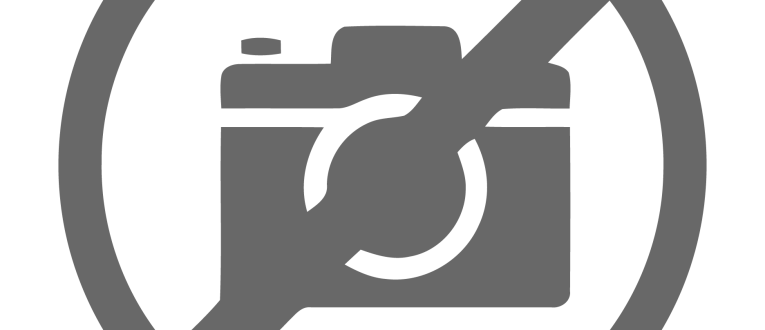
Endumax In Non-Woven Sheets
Sheets and rolls of Endumax are available with different thicknesses that range from approximately 105 to 250 μm (a bit more than 4 to 10 mil). Each single-layer unidirectional material (in approximately 55-μm thickness) is laminated to a HPDE matrix film as the binder.
Since Endumax and HPDE are in the same polyethylene family, they bond strongly together. As unilayer materials have all their strength in one direction, speaker applications use two or more laminated crossply polyethylene film layers. The two-, three-, four- and five-layer materials become cross-ply when the tapes are positioned in 0° and 90° and pressed, together using a HDPE matrix film (see Table 2).
Woven Endumax
Polypropylene/Endumax woven is another option and this hybrid woven material costs less than 100% Endumax. It is also easier to form. The 100% Endumax woven material is considered a premium woven material without the polypropylene additive and is used for the lightest and strongest and highest Young’s modules applications.
Short-Cut Fibers
Paper cones made from the wet laid cellulose (paper) fiber process will remain the best speaker cone materials for the foreseeable future. Yet, additives ranging from New Zealand pulp and kapok to Teijin Conex aramids to Kevlar and carbon fiber have significantly advanced composite formulations. Endumax short-cut fibers added to the cellulose paper slurry during the beating process can improve the Young’s modules, stiffness, reduce intermodulation distortion, and enhance damping.
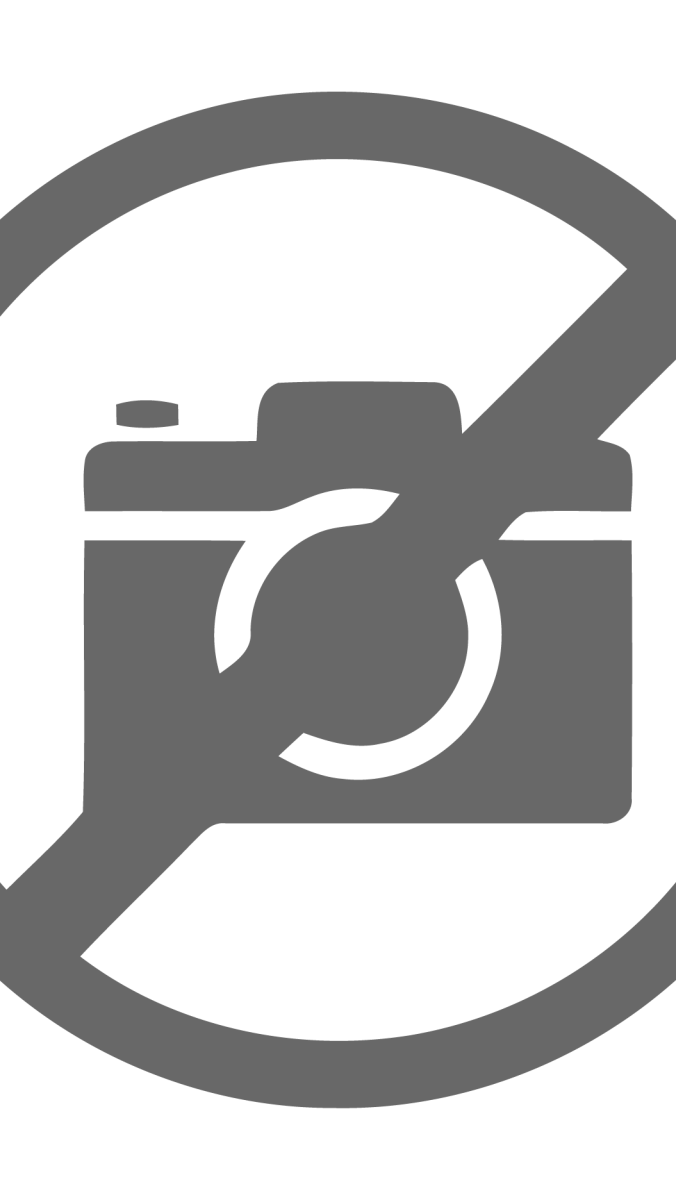
Endumax is just entering the speaker industry supply chain. Dr. Kurt Müller GmbH & Co. KG (DKM) of Germany is the leader in paper cone technology and is finalizing the development of Endumax cones (see Photo 4).
Sea Galleon is the exclusive distribution agent for China and Kou Ryou is the agent in Taiwan. The leading cone manufacturers are perfecting the forming process for this material and sample cones will soon be available from the distribution agents and various cone companies, which means Endumax will also become available to the speaker industry. Details for production yields in forming, optimized application of short-cut Endumax fibers in the paper cone fabrication process, and the design decisions of direct drop-in for existing designs to take advantage of “from scratch” designs are ahead. VC
www.teijinendumax.com
This article was originally published in Voice Coil, February 2015.