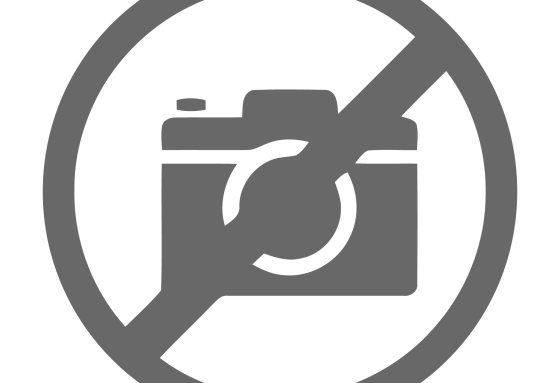
And third, I ran across some low-voltage tubes that were designed to run off the battery voltage in car radios.
My goal in designing this amp (Photo 1) was to come up with an easy-to-build, affordable project that’s safe and fun for an inexperienced builder to experiment with. I wouldn’t call it a high-end audio design, but it does sound pretty good. You can use it as a headphone amplifier or as a line amplifier to drive power amps.
This amplifier uses a single-ended tube voltage amplifier stage and a solid-state follower to get a low enough output impedance to drive headphones. It uses no negative feedback. I think this type of circuit is a good introduction to the sound of tube audio equipment.
Low-Voltage Tubes?
Most tube audio circuits—even low-level preamps—operate on power supply voltages of between 100 and 500V. With proper precautions while building and working on your equipment, these voltages really shouldn’t be a safety hazard—but nevertheless, they can deter the inexperienced from attempting to build tube equipment.
Most audio experimenters probably don’t know that there was an entire line of tubes designed to be operated from a low-voltage power supply.
These tubes, sometimes called “space charge” tubes, were designed during the transition from tube to solid-state electronics, mostly for use in 12V DC automobile radios.
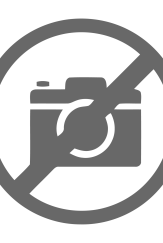
triode/dual diode tubes
12AE6A (left) and 12FM6.
When transistors were first commercially available, radio-frequency transistors were expensive and difficult to manufacture, so hybrid tube-transistor car radios were developed. Most often, these radios employed tubes in the RF and low-power audio stages, and a germanium power transistor to act as the final audio stage, to drive the low-impedance loudspeaker. This hybrid low voltage tube plus transistor approach was used only for a short time before fully transistorized radios became cost-effective, making the hybrid low-voltage tube radios obsolete.
Because of their target application, many of the low-voltage tubes are RF tetrodes and pentodes. Fortunately for us tube audio fanatics, there is also a whole line of tubes that contain a small signal audio triode plus two diodes.
These tubes were used as the detector, AVC, and first audio stage in a typical AM radio. This is the type of tube I used in this design. There are several interchangeable types to choose from, and they are inexpensive and readily available.
Two such tubes, a 12AE6A (left) and 12FM6, are shown in Photo 2. The headphone/line amplifier presented here takes a similar approach to those old car radios: a low-voltage tube is used to amplify the audio signal, and a solid-state output stage is used to provide a low-impedance drive for headphones or a power amplifier.
The Circuit Design
Refer to the schematic diagram (Fig. 1), as I walk you through the circuit and describe how it works.
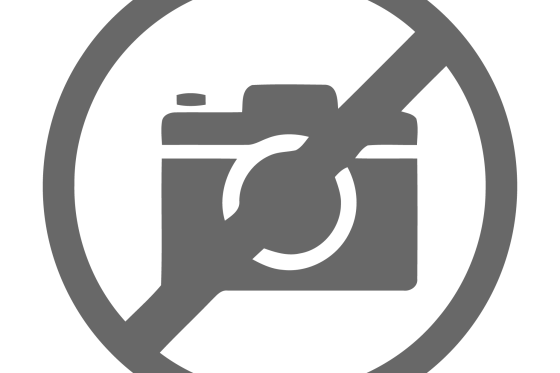
Input Stage
The audio input from J4 is fed to a 50kΩ volume control potentiometer, RV1. The output of the volume control is connected directly to the tube’s grid, so the DC voltage on the grid is 0V. The triode of a space-charge triode/dual diode tube is used in a normal grounded-cathode voltage amplifier circuit.
There are several such tubes that you can use; I tried the 12AE6 (or 12AE6A) and the 12FM6. Other tubes that may work, and all with the same pinout, include the 12AJ6, 12EL6, 12FK6, and 12FT6. Since the diode sections are unused, they are simply tied to ground. Bias for the tube stage is developed across an adjustable resistor (R2, R6), which is paralleled by both an electrolytic capacitor and a film capacitor.
DC current flowing through the tube raises the cathode voltage above the grid, which provides negative bias for the tube. The capacitors provide a low impedance path for the audio signal.
Note that the exact value of these capacitors is not at all critical.
The plate of the tube is loaded with a 0.56mA constant-current diode (D3, D4). You can think of this part as a resistor, which varies its resistance to try to keep a constant current flowing through it. The effect of this is to present a very high AC impedance load to the plate of the tube, which allows the tube to operate at high gain and low distortion. It also allows the plate to swing very close to the power-supply voltage.
There’s nothing sacred about using 0.56mA as the plate current—looking at the plate curves, I thought it looked like a good point to operate the 12AE6 tube.
I also tried a 1mA part, and got slightly higher distortion. You may want to try different currents, especially if you use tubes other than the ones I tried.
You can also experiment with using a resistor in place of the constant-current diode as a plate load. I tried resistors in the 47k to 100k range. I found that I achieved lower distortion and higher output levels with the constant current diode. I didn’t do extensive listening tests with the resistor load, though.
The DC voltage present (with no signal) on the plate of the tube varies, depending on the setting of the bias resistor.
I’ll discuss this setting in detail later, but normally this voltage is between 12V and 20V.
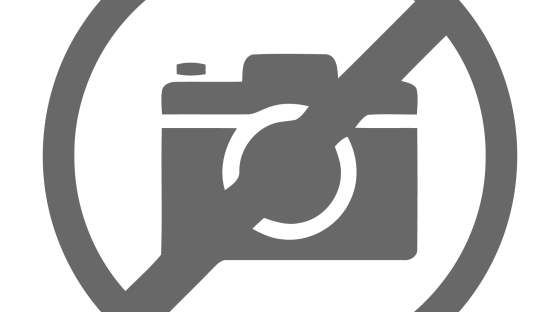
Output Stage
The plate of the tube is directly coupled to a unity-gain buffer amplifier IC, the BUF634, which is made by Burr Brown (now Texas Instruments).
The BUF634 is a follower, meaning that it has no voltage gain; the output voltage is the same as the input voltage. It has very low output impedance, and can provide up to 200mA of current from its output. Its input impedance is very high, so it doesn’t load the tube stage significantly.
For those familiar with the BUF634, this application seems a bit strange.
The typical use of the BUF634 is to be connected to the output of an op amp to boost its current capability. Normally, it is placed inside a feedback loop and is powered with bipolar (positive and negative) power supplies. Here, the BUF634 is used as an open-loop buffer, powered with a single positive supply.
The DC coupling to the plate is required to provide the DC bias needed for the BUF634 to operate.
Normally, with no connection made to the BW pin, the BUF634 operates in a very low quiescent current mode. If you desire, you can operate the BUF634 in a wide-bandwidth, high-bias mode, by connecting the BW pin to ground (at JP1 and JP2). This lowers the open-loop distortion of the part ever so slightly.
The difference in THD is barely measurable, but I found that the character of the distortion did change. In the high bias mode, I saw fewer odd harmonics.
This is the mode that I used, but feel free to experiment with both settings.
The output of the BUF634 is connected through a 22Ω resistor, which is needed only to help protect the BUF634 in case of a short circuit of the output, but it also affects how different headphones sound. I usually recommend a series resistor of between 10% and 50% the impedance of your headphones — e.g., if you have 200Ω headphones, use a resistor between 20 and 100Ω. If you don’t know what impedance your headphones are, or are going to use several different headphones, stick with a smaller resistor (such as 22Ω). Again, you can experiment with this resistor value to see what differences you hear without worrying about hurting anything. For line amp use, the value of the resistor makes very little difference.
Since the BUF634 is being operated with a single-ended power supply, its output sits at a DC voltage above ground (the same as the tube plate). To connect to headphones or other audio equipment, the DC must be removed with a coupling capacitor. I used an audio-grade 100μF electrolytic capacitor, paralleled by a small film capacitor.
The exact value of these caps is not critical, but it does set the low-frequency response limit of the amplifier. For most headphones, anything over 47μF is adequate. The output side of the capacitors then connects to both the headphone jack (J1) and an RCA line output jack (J3).
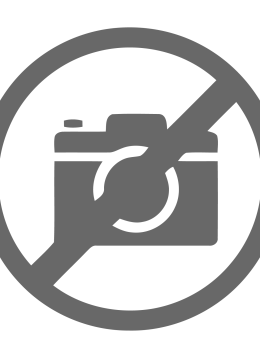
(PCB size: 4.75″ × 6.75″)
Power Supply
Input power is provided by a 24V DC wall-mount supply through the DC input connector, J2. By using an off-the-shelf DC wall adapter, there’s no AC line voltage present anywhere in the headphone amplifier, so it’s very safe. The supply does not need to be regulated; any voltage between 20V and 28V is fine.
The DC power is controlled by the power switch S1, and then flows through a PTC fuse device, PF1. This device is like a fuse, in that when too much current flows through it (in this case, over 500mA), it becomes an open circuit, stopping current flow. It is different from a fuse in that once it has a chance to cool off, it recovers and closes the circuit again.
D2, which is connected between the PTC fuse and ground, is a 30V
transient protection diode. Forward biased (anode positive), it conducts current like a normal diode; reverse biased (anode negative), it does not conduct until 30V is exceeded, at which point it conducts. The purpose of this device, in conjunction with the PTC fuse, is to protect the circuit from the connection of a DC supply that either is wired with the wrong polarity or exceeds 30V. In either case, the transient protector will conduct, essentially shorting the supply, which will cause the PTC fuse to open.
A power-on LED, D1, and its current limiting resistor, R1, provide a visual power-on indicator. C1 acts as a filter, helping lower noise and hum coming in on the DC power.
The 24V DC power is applied to the filaments of the two tubes, which are connected in series. As long as the two tubes are the same, each filament will get one half of the 24V supply, or 12V. Note that the tubes designed for car radios are designed to work correctly with any voltage between 10 and 16V on their filaments.
The 24V DC power is also used to provide power to the two BUF634 amplifier ICs. This power is decoupled, or filtered, with several capacitors in parallel — an electrolytic capacitor, a film capacitor, and a ceramic capacitor.
The reason for this is to provide a low impedance over a wide frequency range to the IC. Each type of capacitor has a low impedance over a different frequency range, and paralleling them accomplishes this.
Power for the voltage amplifier tube stage is further filtered by a 1k resistor and another 100μF electrolytic capacitor, paralleled by a small film cap. The tube stage is sensitive to hum or noise on the power supply, so this filter prevents any ripple or noise present on the supply from being amplified and appearing at the output. The decoupling also prevents any feedback from the output stage to the input stage caused by perturbations of the power supply.
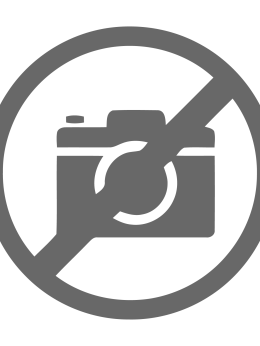
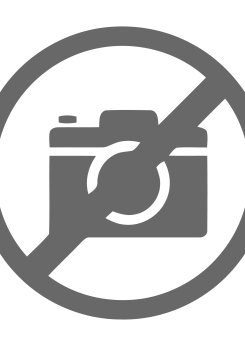
Since my goal with this project was to do something that would be easy to build, I designed a printed circuit board (PCB), which contains all of the components, including input and output
connectors and the volume control (Photo 3).
Assembly
Assembly is a simple matter of inserting the components into the PCB, soldering the leads to the board, and trimming any excess wire from the back. Make sure that you install the electrolytic capacitors capacitors and diodes in the right orientation, matching the designation on the PCB.
The BUF634 buffers are bolted to small PCB-mount heatsinks. I found that even in high-bias mode, they run barely warm to the touch during normal operation, but the heatsinks will help protect the part in the event of a short-circuited output.
Since there are no dangerous high voltages present, I designed the PCB to mount into one half of an inexpensive plastic instrument case, with the top side of the PCB exposed. I just mounted the board into one half of the enclosure and discarded the other half (Photo 1).
This made a simple, easy way to mount the PC board, and still allow access to the board to adjust bias, change tubes, and make measurements. You could also mount the PCB into a more conventional metal box if you choose.
Once the PCB is assembled and mounted to the plastic case, all you need to do is install the tubes into their sockets, plug in the power supply, and adjust the tube bias as detailed later. Of course, the more experienced builder could also build this project using conventional point-to-point wiring inside a chassis.
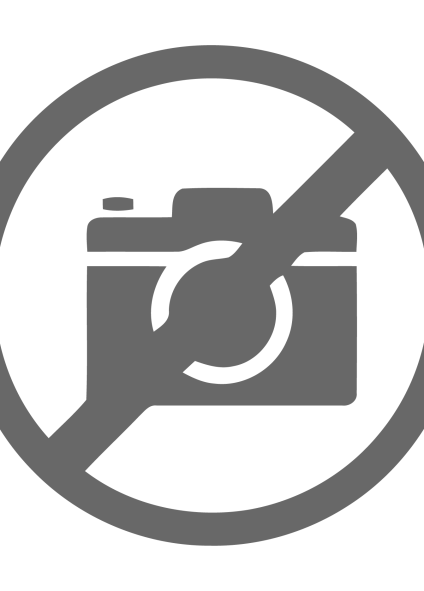
Parts
I used only parts that are readily available for a reasonable cost from mail order distributors that cater to hobbyists.
Table 1 is a listing of all the parts used, where I purchased them, and about what they cost. Refer to the contacts listing at the end of the article for information on how to get in touch with the vendors listed.
The parts list is all-inclusive, including the plastic enclosure, volume control knob, and so on. You can see that the entire project can be assembled for about $100. The only tools you’ll need are a screwdriver, wire cutters, and soldering iron. You’ll also need a voltmeter (any analog or digital meter will do) to set the bias, which I’ll describe later.
Exact part selection is not at all critical.
Capacitors should be rated for at least 50V, except the cathode bypass capacitors, which can be rated as low as 16V. Capacitance values can vary between about 50% and 200% of the values I used with little change. Resistors, too, can be anything close to what I used with not much effect.
The PCB
Figure 2 shows the top side of the PCB, showing parts placement. Figures 3 and 4 are the top foil and bottom copper foil layers. You can also download the artwork files from the author’s website at: www.pmillett.com.
Setting the Bias
I decided to make the bias voltage for the tubes adjustable, partly so you could easily try out different tubes, and partly so you could try different operating points for the tubes. Since the bias voltage is just developed across the cathode resistor, making this resistor a trimmer potentiometer provides an easy way to vary the bias.
If you measure the voltage at the output of the BUF634 with no audio applied (which is the same DC voltage as on the plate of the tube), you can set the operating point of the tube by adjusting the bias trimpot. Measuring at the output of the BUF634 guarantees that the voltmeter won’t load the voltage on the high-impedance plate.
Since the plate load is a 0.56mA constant-current diode, moving the bias point around does not affect the plate current. If you substitute a resistor for the constant-current diode, you can still adjust the bias in the same manner, but the plate current will vary with the bias setting.
Setting the bias is a great way to experiment with the “sound” of different tube distortion. For example, as you adjust the bias to get a progressively lower plate voltage, you get more and more “single-ended” second harmonic distortion.
As you raise the voltage to one half the supply voltage, you can get a higher output voltage before clipping, at the expense of higher third-harmonic distortion at lower levels. Raising the voltage further lowers the distortion products at low signal levels at the expense of a lower maximum output level.
I looked at the distortion products of the output using an audio analyzer, but you really don’t need sophisticated test equipment to set the bias on your amplifier.
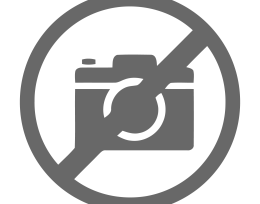
driven to clipping.
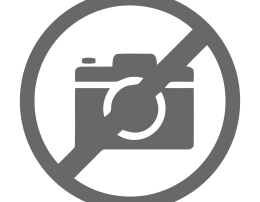
and distortion residual (bottom).
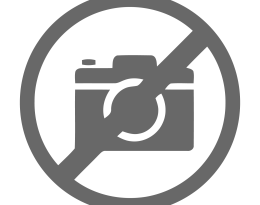
and distortion residual (bottom).
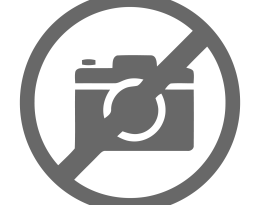
driven to clipping
If you just put a voltmeter on the bias test points, you can adjust the bias based on the DC voltage you measure there. Then, use your ears to evaluate the result. I found that you really can hear differences in sound with changing the bias, especially in low-level detail.
With both the 12AE6 and 12FM6 tubes that I tried, adjusting the bias to one-half the input power-supply voltage provided mostly symmetric clipping, and the highest output voltage. My wall supply was putting out 27V, so I set the bias to 13.5V. Photo 4 shows what the output looked like at this bias setting, using a 12FM6 tube, driven hard into clipping.
Note that clipping is nearly symmetrical, but the top of the waveform is clipped more abruptly than the bottom.
This is the point where the output hits the positive power-supply rail.
Photo 5 shows the output signal and distortion residual (what’s left of the signal after you cancel out the original input signal) for a 1kHz, 1V RMS output with the same bias. The residual, shown at a much higher scale than the output signal, is very nearly a sine wave at a frequency of 2kHz. This indicates that the distortion is primarily second harmonic.
If you adjust the bias voltage lower than one-half the supply voltage, you can avoid the sharp clipping at the top of the waveform—but distortion increases dramatically, since the tube becomes very nonlinear as the grid begins being driven positive with respect to the cathode. If you adjust the voltage above one-half the supply voltage, you can reduce the distortion at 1V RMS out, at the expense of slightly decreasing the maximum output that can be obtained before clipping.
Photo 6 shows the waveform in heavy clipping at a bias voltage of 19V. You can see that the top of the waveform is more clipped than in Photo 4. However, the distortion at 1V RMS out is actually slightly lower (Photo 7). I found this bias setting to be much more pleasurable to listen to than the lower plate voltage bias point.
Circuit Performance
For those not used to tube circuits, the distortion figures that follow will seem large. Indeed, this is not a low-distortion amplifier, but THD alone is not much of an indicator of perceived sonic performance. In fact, I believe that much of the appealing sound of a single-ended triode amplifier has to do with the introduction of second-order harmonics into the music. That’s one of the purposes of this project—to allow you to listen to, and experiment with, this distortion.
I made distortion measurements of the amplifier, using both a 12AE6A tube and a 12FM6 tube, at two different bias settings, both using a 0.56mA constant-current diode as the plate load.
Here are the results:
12AE6A, bias = 13.5V
Maximum output at clipping: 2.7V RMS
Maximum output, 5% THD: 1.8V RMS
THD, 1V RMS out: 0.6%, largely third harmonic
12AE6A, bias = 19V
Maximum output at clipping: 2V RMS
Maximum output, 5% THD: 2V RMS
THD, 1V RMS out: 0.5%, virtually all second harmonic
12FM6, bias = 13.5V
Maximum output at clipping: 3V RMS
Maximum output, 5% THD: 2V RMS
THD, 1V RMS out: 1.5%, mostly second harmonic
12FM6, bias = 19V
Maximum output at clipping: 2V RMS
Maximum output, 5% THD: 1.7V RMS
THD, 1V RMS out: 1%, virtually all second harmonic
The relatively low maximum output levels are limited by the low plate voltage used on the tubes. You can experiment with different tubes, different bias settings, and different constant-current diodes, and probably find operating points different than the ones I used that may provide higher output, and/or lower distortion.
For most headphones, the output from this amp is adequate to drive to quite loud listening levels. With Sennheiser HD600, Beyerdynamic DT831, and Grado SR60 headphones, there was ample output before distortion to well beyond the loudness that I can tolerate. This was verified both by ear and by looking at the waveforms to verify that the amp was not driving anywhere near clipping.
With my AKG K240 headphones, the amp couldn’t drive as loud before reaching the onset of clipping. These are 600Ω impedance headphones, which require quite a lot of voltage. I would say this amp was marginally acceptable driving them.
Just for comparison, I measured the output level at the headphone jack of two portable CD players. With the first unit, a brand new midrange player, I could not drive the headphone output to clipping. The maximum output level, with a 0dBFS test CD, was 0.4V RMS. I could drive the second CD player, an older and more expensive unit, into hard clipping at 3V RMS.
As a line amplifier, the output of this amp should be more than adequate to drive all but the most insensitive power amps. Its low output impedance should be able to drive just about any interconnect cable.
The frequency response measured very flat, within ±0.1dB from 20Hz−20kHz, into a 200Ω load. At 100kHz, the limit of my audio analyzer, the output was down only 0.8dB. Into a lower impedance load, the low-frequency response will drop a little, since the output is coupled through a capacitor. With the 100μF capacitor I used, you can expect about −3dB into a 30Ω load at 20Hz.
I measured the noise at the output (terminated in a 200Ω load) with no input signal at 200μV. This was an un-weighted measurement, which corresponds to −74dB below 1V RMS, very near the measurement limit of my test setup. This is very quiet for a tube amplifier.
Conclusion
I’d be lying if I were to tell you that this is the best-sounding headphone amp I’ve ever listened to. But I’ve listened to dozens of headphone amps, some of which cost more than the average new car. This amp does well, considering its cost and the design compromises I made. It will certainly be an improvement over what you would hear with headphones plugged into a portable CD player. And being a fan of tube sound myself, I think it sounds a whole lot better than one of those $350 “op-amp in a wooden box” audiophile headphone amps.
The main goal with this project is not to build a headphone amp, but rather to build a project that can be a positive learning experience for someone who’s just getting started with building and designing audio equipment. I think from that perspective, this design is a success: It’s an easy, inexpensive project that will allow you to experiment with the sound of tubes.
References
Tubes, tube sockets, capacitors, and so forth.
www.tubesandmore.com
www.thetubestore.com
www.watfordvalves.com
www.tubedepot.com
vacuumtubesinc.com/Default.aspx
www.tubeworld.com/index_high.htm
www.abcvacuumtubes.com
www.tube-town.net/ttstore/
www.drtube.com
www.hotroxuk.com
www.eurotubes.com/store/pc/home.asp
www.dougstubes.com
www.commonsenseaudio.com
www.kcanostubes.com
www.nostubestore.com
www.tubemonger.com
www.thetubecenter.com
vacuumtubesupplies.com
www.tubeworld.com/index_high.htm
www.nosvalves.com/sale.htm
www.btb-elektronik.de
Welborne Labs—resistors, capacitors, audiophile parts, and so on.
www.welbornelabs.com
Full-line parts distributors
www.partsconnexion.com
www.parts-express.com
www.digikey.com
www.mouser.com
Pete Millett
www.pmillett.com − The author’s web site, where you can download full-scale drawings of this project.
This article was originally published in audioXpress magazine, November 2002.
The author's website already includes updates and optional improvements to the original project.