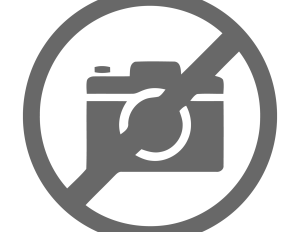
Beyond enabling bigger speaker drivers into smaller enclosures, acoustic resistance meshes also are powerful tools to optimize transient response. Controlling the acoustic resistance of the driver radiation is a quality factor that is overlooked in most loudspeaker predictive modeling software.
Settling time of adjustments was a basic consideration in the original works of Benson, Novick, and Thiele. Acoustic resistance can be obtained from both woven and non-woven filters. Wovens are selected for repeatability and for uniformity, with maximum deviation of less than 10%. When cost is critical non-wovens are selected. Yet in an earphone or headphone, the non-woven material contributes more variation in production in the bass than even the driver.
Non-wovens vary over 30% in acoustic resistance, and characteristics change with humidity. Open a Sennheiser headphone — even their lower-end models — and you will see mesh, not non-woven membranes. Yet lower grade mesh that absorbs moisture can pick up dust and become clogged, so hydrophobic-treated mesh is a beneficial requirement for stable long-term characteristics.
In the specific case of speakers and speaker systems, acoustic resistance may take the physical form of a woven fabric tensioned onto either the windows of the woofer frame and/or on the bass reflex vent opening. The interaction with the performance is different for damping the driver versus damping the enclosure, with damping the driver itself being preferred.
This article — including the sidebar profile of Saatitech, the specialist vendor of acoustic resistance materials — explores applications of acoustic resistance for audio. Acoustic resistance is the opposition to the flow of sound through a surface such as a mesh or nonwoven membrane.
Readers will recognize common examples of acoustic resistance meshes such as mike wind screens, but speaker applications are more obscure, such as meshes over vented pole pieces or meshed covers on the frame for venting behind the spider on woofers and aperiodic bass reflex venting in enclosures and mesh over vents in headphones. Of course, most mikes and cellphones have wind screens. The variovent (Photo 1) consists of two grilles with some damping material stuck in between. The diameter, amount of damping material, and the compression of the material determine the air flow properties, and thus acoustic resistance.
To start at the beginning, a tightly precision woven mesh provides “dialed in” uniform acoustical resistance. A path between the front and back radiation provides an acoustical short circuit. Placing a mesh over a vent hole results in a partial short circuit — i.e., there is some (acoustical) resistance. Using an electrical circuit filter analogy (such as Thiele/Small parameters), acoustic mesh can be modeled as a “resistor” across an inductor or capacitor or other tuned circuit. The application of acoustic mesh can improve impulse response settling time (damping).
As you would expect, when the Q factor is damped, then less than maximally flat response results. Q is a term with beginnings in radio frequency (RF) design, with the peaking of the inductor characteristic being the Quality figure of merit. For sound reproduction a very high Q peak is not necessarily what we are looking for. Acoustic mesh is a design tool to widen the bandwidth of the Q.
Surface-treated acoustic mesh can provide benefits outside of acoustics, such as water penetration resistance in mobile phones, outdoor mikes, and speakers. Conversely, mesh that is treated for wetting can absorb binder resins, such as for spiders, fabric surrounds, woven high performance fiber cones, or tweeter domes.
Practical Aspects and Implementation of Acoustic Impedance
The tighter the mesh aperture (opening), the higher the acoustic resistance damping and the greater the loss of low-end response. The more open the mesh weave, the more acoustically transparent the mesh. If the electromagnetic control of the driver at resonance is not sufficient for a given enclosure and tuning, then for some misalignments you end up with a high-pass response characteristic of a sharp response peak before the output takes a dive. Conditions such as speakers that are crammed into too small bass reflex or lossy enclosures are common offenders. Acoustic resistance damping is far less expensive than overmotoring through electromagnetic damping!
While a sealed acoustic suspension enclosure can provide tight linear control using an “air spring,” it is at the expense of sensitivity or bass extension. Ideal bass reflex solutions are often too large or require pricey magnetic structures to adequately motor the design. To tweak the bass reflex alignments that are too compact and to keep woofer cost within budget can often benefit from acoustic resistance. Acoustic resistance used on the back frame of a driver or bass reflex vent is a gray area between sealed and vented solutions.
Consider the following half-dozen applications in which acoustic resistance is a valuable design technique.
Bass Driver Cavity Venting
For ventilation cooling, many woofers vent the pole piece and/or the cavity under the spider. QC personnel checking woofers on the production line will recognize the phenomena of higher buzz and rub in less than perfect units when the unbaffled woofer is tested dangling in the air (such as holding the woofer in your hands while you test), but when placed on a table the buzz and rub goes away.
Various factors account for this — one is the slightly reduced excursion when the vent is blocked (by the table). But mostly the blocked vent produces an “air bearing” which minimizes scrapes. You can retain venting while maintaining some of this air bearing effect by selection of the proper “acoustic impedance mesh.” Another related phenomenon is the chuffing of the vented pole piece — due to the air velocity reaching turbulence. The mesh across the vented pole piece drops the volume of air which will reduce the vent noise (of course, also cutting down on the cooling).
Microspeakers, balanced drive tweeters, and headphone drivers mostly have similar topology. Specifically, centering during assembly is on the periphery of the surround, with a one-point suspension (no spider) being the compliance corrugation at the edge of the cone. At higher excursions the voice coil tends to rock and there is little restoring force.
In the case of earphones and headphone enclosures, there are typically front and rear vents. If there is a headphone enclosure (earcup) venting positioned in front of the diaphragm, the bass will “evaporate” unless you use an acoustic resistance mesh. The acoustic mesh enables the use of a larger vent hole without loss of bass.
Selection of the degree of acoustic resistance controls the trade-off between bass output versus settling time (damping).
Then there is the issue of non-wovens versus monofilament mesh. It is the nature of non-wovens to have very wide variation — not just roll to roll, but within the roll itself. Non-wovens are usually hydroscopic and change characteristics with humidity.
Acoustic meshes can be precision materials with uniformity of well over 90%, so when an optimum mesh damping is determined, the production is repeatable. In microspeakers and headsets one of the key variations is the damping fabric, and just by shifting to precision meshes the lower octave response variations tighten up dramatically.
Using acoustic resistance can improve settling time in planar ribbon and electrostatic speakers. With the mesh behind the planar, a thin evenly distributed air cushion will reduce the settling time of the tensioned diaphragm. At resonance, tensioned diaphragms act like a plucked guitar string and the mesh damps the decay.
Non-Acoustic Applications of Mesh
Totally unrelated to speaker driver and enclosure characteristics is the application of precision meshes for grille cloth. The higher acoustic impedance meshes with smaller openings (tighter weaves) provide damping. You can select open weaves that offer complete acoustic transparency.
Compared to conventional fabrics, precision acoustic meshes are consistent, so production run batches are essentially identical. These monofilament polyester meshes are not hydroscopic, so there is negligible moisture absorption or change in sound transparency with humidity. For mobile consumer electronics products such as cellphones, hydrophobic meshes enable venting for sound, pressure equalization and cooling while blocking water.
Many automotive OEMs require meshes on the rear of the speakers for dust and debris protection, and when used in this open back (“free air”) condition there is also an opportunity for some acoustic resistance benefit. A hint for designers of in-wall speakers: If the in-wall has a back cover, then the internal volume tends to be too tight, but left open the back volume is too large. With acoustic resistance mesh tensioned over the woofer, you can bring this into balance without needing the back cover.
Microphone Applications
The most common application of acoustic resistance meshes is for microphone wind screens. Other applications for acoustical filters for mikes include handsfree car phones, onstar talkback, over-the-ear bluetooth, cellphones, and computer headsets with boom mike. In most cases there is a scrim used in front of the mike—or foam, or foam and felt.
For full waterproof applications there is composite mesh with a thin film lamination that fully meets IP 47 and 48 with nominal wideband acoustic loss.
Up to three layers of different meshes can be used on outdoor, stage, movie, and electronic-news-gathering (ENG) microphones to block wind, rain, or debris. Special mesh metalizing treatments also block electrical noise (EMI) and electrostatic discharge (ESD). In directional mikes, meshes can be used for “tuning” back chamber baffling to smooth and widen back of mike sound rejection.
While acoustic mesh has been a common design technique in European mikes and headphones for decades, acoustic resistance has only recently become a consideration of experienced speaker engineers. Aside from the acoustic contribution, precision meshes are a unique solution to keep rain off outdoor speakers, wind and spit out of microphones, and debris from the back of car door speakers.
Article originally published in Voice Coil, May 2011
Saatitech – Acoustic Mesh Specialist